广州思林杰网络科技有限公司,面向在线自动化测试的嵌入式仪器专家,专注于开发和生产工业自动化设备,主要产品为自主研发的嵌入式仪器。
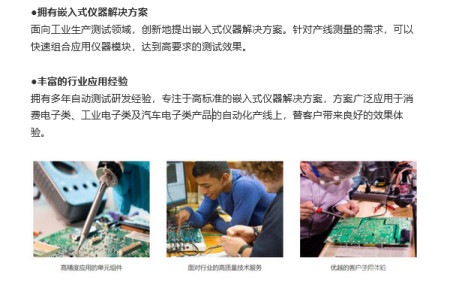
01引进E10+PLM,缩短订单交付周期
进入互联网时代,面临管理挑战更大,企业的成长目标更为明确:
1.提升组装生产所需物料配套能力,减少停工待料,提升生产效率;
2.提升车间整体生产运营能力,通过缩短订单交付周期来提升效率,增加营收。
“缩短订单交付周期”更是成为企业迫切需要实现的关键指标,携手鼎捷软件引进E10+PLM,希望透过缩短订单交付周期实现企业的管理蜕变。
02一体化成效显著,实现转型升级
经过我们软件信息化项目的上线努力,企业方面表示E10以及PLM实现了管理升级,并为后续的经营策略提供了必要的支撑,基础指标达成状况如下:
1.BOM资料准确度>99%
2.存货结账时间<10天
3.库存准确率>95%
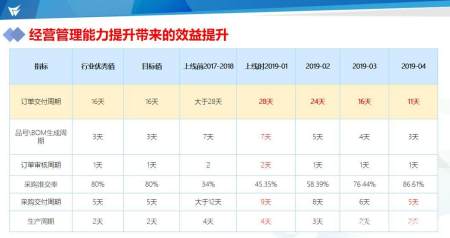
可以看到:上线前2017-2018年企业的订单交付周期大于28天,2019年系统上线后订单交付周期缩短至11天,意味着合作信息化项目之后,整体订单交付周期缩短了17天。
03 E10:6大管理典范铸造过硬管控能力
1.提升硬件设计能力
硬件设计周期:7天->5天
上线前:
1.电子元器件品类繁多,分类复杂,利用率非常低;
2.没有电子元器件申请、承认机制;
3.没有电子元器件优选机制;
4.硬件原理图与BOM脱节;
5.电子元器件符号库管理与物料管理脱节
上线后:
1.电子元器件分类清晰,物料编码、名称、规格描述规范;
2.统一的电子元器件库管理;
3.建立电子元器件优选机制,工程师能够快速选用企业最优的器件;
4.电子符号库与物料集成管理;
5.直接从原理图产生BOM
改变了什么?
建立电子元器件优选库;
建立电子元器件优选机制;
固化物料申请、认证流程;
提升物料标准化,减少一物多码,降低库存成本,提高产品设计质量
2.提升BOM产出能力
BOM产出周期:1天->0.5天
上线前:
1.清单式传递,清单上描述不清楚,原理图所用元器件与物料不完全匹配;
2.专员录入ERP系统,效率低,容易出错
上线后:
1.原理图设计完成,即产出PCBA的BOM,运用Cadence集成工具直接生成准确的BOM;
2.固化BOM审核流程
改变了什么?
重建产品设计作业模式;
引入产品生命周期管理;
规范产品设计流程;
缩短BOM产出周期;
提高产品设计质量
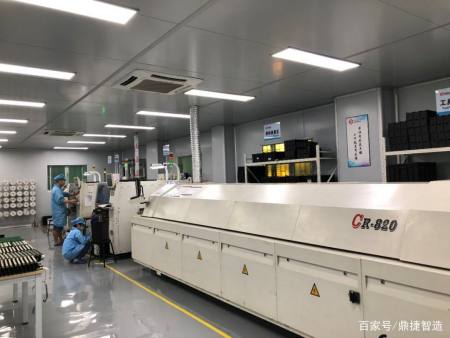
3.提升基础资料协同能力
基础资料同步周期:无->5min
上线前:
1.产品生命同期资料不齐套,难以查询,难以收集;
2.设计过程难以选择最优物料,难以获取物料库存、价格等信息;
3.设计结果需要人工传递,BOM需要手工转换与录入
上线后:
1.产品生命周期资料在同一平台上管理,并与产品进行关联管理,多维度快速查询物料与其关联文档;
2.设计过程可直接查询库存、价格等信息,以选择最优物料;
3.设计结果统一在PLM管理,下游部门直接在ERP可直接查看PLM图纸,BOM直接从PLM传递给ERP
4.提高订单处理能力
订单评审周期:2天->1天
上线前:
1.订单评审流程为逐级签核,由商务部下发到跟单,由跟单发起评审-研发-NPI-供管-生管等签核,一环扣一环,导致评审周期过长;
2.没有价格体系,每次报价需要采购部与财务共同计算产品价格,花费时间长
上线后:
1.订单评审流程优化,在系统中建立签核流程,逐级签核变更为并行:由跟单发起评审,其他部门同步评审;
2.建立标准价格体系,若为新产品则通过BOM成本模拟,快速取得成本报价
改变了什么?
订单评审流程的优化有效的缩短了评审周期:2天-1天;
搭建了产品价格体系,得以快速报价
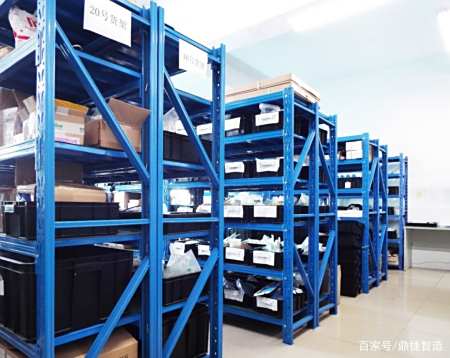
5.提升物料供应能力
采购周期:15天->5天
上线前:
1.连接器、钣金、金属类模具、注塑类模具等的采购周期、送货频次、供应商MOQ等基础参数不明确,物料齐套跟进非常困难,靠经验判断跟进效率低;
2.IC、半导体、变压器、继电器等采购周期长,预测不到位,导致无法按订单需求准时到货
上线后:
1.梳理物料采购周期、送货频次等,保障下单及回料交期准确;利用料件需求检视表协助采购员及时跟进供应商回料;
2.建立产销模型和存货策略,制定PCBA半成品长周期滚动月度预测
改变了什么?对长交期关键料根据半成品预测生成采购计划下发;
制定物料备货方式、采购周期等,按计划进行采购,覆盖范围更全面;
采购预警,及时跟催
6.提升组装生产制造能力
组装周期:3天->2天
PCBA制造周期:5天->3天
上线前:
1.生产计划覆盖周期为1个月,不停的根据生产或商务的反馈调整排产表,重复工作多,每日耗费4小时做调整;
2.排产时,无物料齐套分析工具,欠料分析每日需耗用2小时以上,效率低;
3.组装物料齐套率低,导致成品无法组装,等料次数每周至少2-3次;
4.SMT线生产计划与生产线计划脱节,往往在组装时才发现SMT线的PCBA板没有生产完成,导致需要调整排产计划,临时变更次数多
上线后:
1.生产计划覆盖周期为2周,根据排产计划指导物料计划提前下达,减少计划调整时间;
2.工单下发前做齐套及欠料分析,计划变更频次降低为0,与SMT线共同排产,从而达成生产线的计划达成率;
3.通过工单管理进行物料齐套分析及欠料分析,10分钟内掌握生产线欠料情况并进行欠料跟催,等料次数降低为0,提升组装生产准时开工率;
4.通过生产预测对PCBA板进行预测生产备库
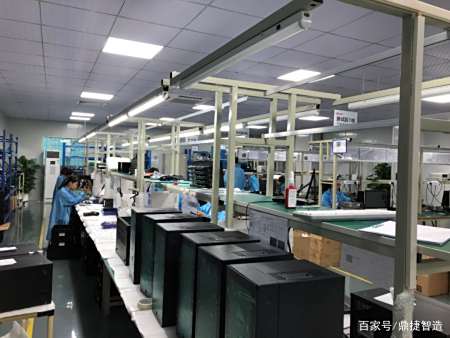
改变了什么?
对共用PCBA板提前进行生产预测备货,有效缩短交付周期2天;
组装车间SMT与生产线共同排产,避免生产脱节造成停工待料的问题
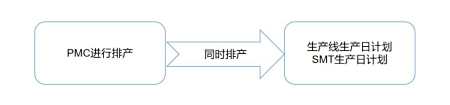
04 PLM:体验研发生产一体化的奥妙
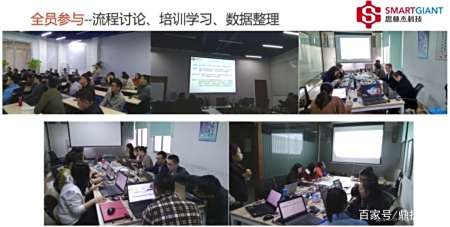
1.器件优选
建立电子元器件优选库:统一管理元器件,建立优选机制,规范器件承认流程,杜绝未承认器件进入中试。提高物料重用率,降低质量风险。
2.提升协同
提升设计生产协同能力:CIS+PLM+ERP,提高器件选用规范,杜绝禁用器件被选用,产品数据无缝传递到生产,提高整体协同效率。
3.变更管理
缩短变更影响分析周期:以PLM为统一的数据管理平台,建立与物料为核心的数据网,快速、准确定位变更影响范围。
4.知识沉淀
建立研发知识库:统一的研发数据管理平台,知识共享平台,以规范的流程确保产品资料齐套性,逐渐形成产品研发知识宝藏。
05研发生产一体化如何实现?
1.通过搭建开放共享的数字化平台,实现全过程的信息化管理;
2.以研发设计生产一体化协同管理模式提升供应链运营质量与效率;
3.以信息化技术促进管理全方位创新与提升。
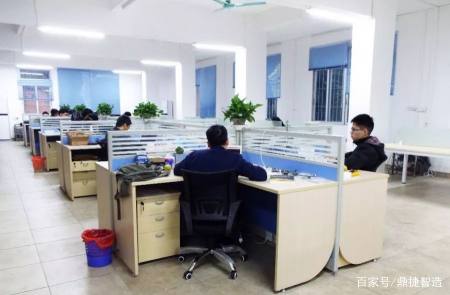
经过信息化项目合作,企业借助E10 ERP以及PLM的全面实施规划,在物料管控、订单评审、车间计划排产等方面逐一攻破管理瓶颈,有效提升了订单处理、物料供应、组装生产制造等多项核心能力。
发表回复